Conventional rubber production for tires relies heavily on synthetic rubber, primarily petroleum-based. It’s one of the largest sources of carbon emissions within the automotive sector. Reselo has stepped up to solve this challenge by creating a rubber alternative using birch bark.
The startup can extract a compound called suberin from birch bark that can be turned into a synthetic-rubber-like material with identical properties. This process reduces carbon emissions related to rubber production by 90%.
The process is a fully sustainable and scalable option for the automotive industry, providing a much-needed alternative to fossil-based rubber. We interviewed Henrik Otendal, CEO of Reselo, to understand their innovation in greater detail.
This interview is part of our exclusive Scouted By GreyB series. Here, we talk to the founder of innovative startups to understand how their solutions address critical industry challenges and help ensure compliance with industry and government regulations. (Know more about startups scouted by GreyB!)
“Instead of burning the birch bark waste, which generates harmful CO2 emissions, we’re turning it into a valuable resource that reduces carbon emissions and contributes to a circular economy.”
– Henrik Otendal
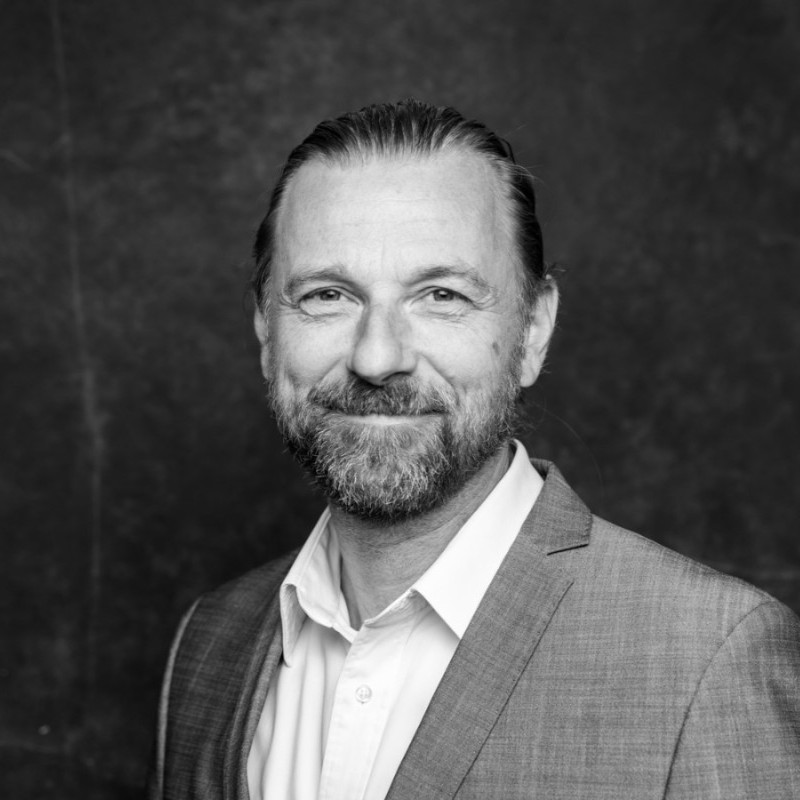
Henrik Otendal is the CEO of Reselo. His professional background is in research and engineering, particularly sustainable materials. Before founding Reselo, he worked on a research project that identified birch bark as a viable material for creating sustainable rubber, which was conducted at the Vallanberg Wood Science Center and KTH in Stockholm. This expertise in materials science and his work on polymerizing suberin from birch bark empowered the company’s product development.
Overview: Turning Birch Bark into Sustainable, High-Grade Rubber
Reselo is a biomaterial startup that has developed a sustainable alternative to traditional synthetic rubber. The company turns birch bark into a high-performance polymer that can replace petroleum-based rubber used in products like car tires, gaskets, shoe soles, etc. This innovation offers significant environmental benefits by reducing carbon emissions by 90% and provides an economically viable solution for the automotive industry.
Watch the entire conversation here:
What makes your birch-based rubber unique compared to existing products in the market?
Henrik: There’s a lot of oil in the world at the moment. But fossil fuel is, ultimately, a finite resource. Eventually, we will all have to switch to alternative materials. That’s where our solution will come in.
At Reselo, we focus on replacing fossil-based rubbers, the most polluting synthetic rubber. We use birch bark because it contains high amounts of suberin. Our proprietary process polymerizes this substance into a rubber-like material 100% compatible with existing rubber products.
Our unique selling point is offering a drop-in solution for the automotive industry. This material product has the same curing process as other rubbers. That means, it can be directly substituted for fossil-based rubber without compromising quality or performance. Tires from our sustainable rubber will have the same abrasion resistance, low rolling resistance, and high friction as fossil-based ones. This is a significant breakthrough because it ensures the transition to a sustainable material is easy and scalable.
What technical or scientific challenges did you face while developing this product?
Henrik: We had some challenges accessing the right equipment, like mixers and blenders. We needed specialized equipment to validate and test our materials, which wasn’t always easy to access. There have been technical challenges, but we’ve successfully developed and adapted the material to fit various applications. It wasn’t necessarily about the material itself, but more about the processes and equipment needed to scale it.
Can you share your approach to scaling your solution and overcoming potential feedstock issues?
Henrik: We are carefully managing the production and ensuring a consistent supply of birch bark for large-scale production. Fortunately, birch is abundant across the Northern Hemisphere, and the bark is often a waste product from the paper and timber industries.
We can currently produce 100 tons in pilot stage, but this needs to increase to meet commercial demands. Our solution is to partner with these mills, offering them a better value for their byproducts. Instead of burning the birch bark, they can sell it to us, creating a sustainable source for our material. This secures our feedstock supply and reduces waste and CO2 emissions, contributing to a circular economy.
What are your plans for future expansion?
Henrik: We are currently focused on scaling our production to meet the demands of our customers. In the near term, we are working on raising funds to develop a larger production facility. We aim to create partnerships with automotive manufacturers and tire producers to get our material into their products.
In the long term, we are also considering expanding into other markets that require rubber-based materials, such as fashion and footwear. We already have production versions of outdoor soles for shoes. Our material is easy to integrate into existing production pipelines for large companies that typically use fossil rubber.
As we grow, we plan to expand globally, starting with regions with strong relationships with timber and paper mills. The various regulatory restrictions on fossil-based rubbers will also work in our favor, making our market entry easier.
What advice do you offer to entrepreneurs facing challenges in their startup journey?
Henrik: I suggest three key approaches for staying motivated. First, communicate daily with your co-founders to debrief, share doubts, and support each other through challenges. Second, regularly look back at what you’ve accomplished to recognize your progress rather than just focusing on new problems. And third, remember to celebrate small victories along the way.
While technical challenges can be solved with a brilliant team, the more time-consuming challenge is often convincing investors of your solution’s value, especially for industrial projects that require significant funding.
Meet our Interviewer
Shabaz Khan, Marketing Manager
To learn more about this startup and validate the effectiveness of its technologies, contact our scouting expert using the form below or explore GreyB’s startup scouting services.