Every ton of steel produced in 2018 emitted 1.85 tons of carbon dioxide on average, equating to about 8 percent of global carbon dioxide emissions.
Studies estimate that the global steel industry may find approximately 14 percent of steel companies’ potential value at risk if they cannot decrease their environmental impact. Moreover, long investment cycles of 10 to 15 years, multi-billion financing needs, and limited supplier capacities make this issue even more relevant for addressing the decarbonization challenge. (Source)
Hence, the decarbonization of steel is vital to meet not only the climate change mitigation targets but also to achieve a sustainable future for the industry. Consequently, steel players across the globe are increasingly facing a decarbonization challenge driven by three key developments.
- Changing customer requirements and growing demand for carbon-friendly steel products
- Tightening of carbon emission regulations
- Growing investor and public interest in sustainability.
It isn’t wrong to say that steel companies implementing technologies to decarbonize their operations may be better placed to capture new market opportunities in the long term. Given the dire need for such a change, this article will cover various pathways and technologies that have given promising results.
While we cover the above topics briefly, you can fill out the form below for an extensive report catering to your need to eliminate the decarbonization challenge for Steel.
That being said, let us hop on to our article.
Which countries are responsible for major CO2 emissions from steel manufacturing?
As we cover the technologies for the Decoarbonization of Steel, the first step is understanding the scale of carbon dioxide emission. To represent the same, Global Energy Monitor has mapped 553 steel plants representing 82% of the world’s installed capacity. Operating steel plants in China account for more than half the global total in this mapping (51%; 1,023Mtpa), followed by Japan (6%; 117Mtpa) and India (4%; 90Mtpa).
It was found that more than 60% of installed steelmaking capacity uses the high-carbon BF-BOF method, in which iron ore is smelted with heat from burning coal, which also acts as the “reducing” agent needed to turn the ore into metal. China’s steel fleet relies on this method, accounting for 62% of global BF-BOF capacity. (Source)
Challenges to overcome to reduce the footprint of Steel Making Industries
At first glance, changing the trajectory of this leviathan business looks like an almost impossible task. Steelmaking has annual sales of $2.5 trillion, according to the World Steel Association, and relies on heavy infrastructures, such as the gigantic blast furnaces that are used to make iron, which can last 20–40 years. It’s pretty difficult to shift a market like steel because there’s so much cost sunk in a blast furnace. However, furnaces in most of the world’s steel plants will reach the end of their investment cycle by 2030, forcing companies to opt for lower-carbon technologies. (Source, Source).
Further, developing countries (like India) rely less on BF-BOF-based processes and more on EAF and mixed methods, emitting relatively less CO2. This shows that India is better positioned to handle CO2 emissions, than countries that use BF-BOF-based processes.
Various pathways for decarbonization of steel
We shall now look at the pathways/technological options the steel industry has at its disposal to manage the decarbonization of the steel challenge. Further, we list the pros and cons of each pathway and the parameters that will help you decide on the right technology.
Alternative to coke in the blast furnace.
The most common steel-making technology is the BF-BOF route. Coke is used in blast furnaces which acts as both – a heat source and reducing agent for reducing iron ore. The majority of the emissions in the steel-making industry come from the blast furnace and the coke plant. In light of the same, recent developments suggest using other alternatives to coke, or substituting some part of coke with other materials can reduce emissions caused by the blast furnace process. Biomass-based, olefin coke, and hydrogen-based blast furnace reduction may emerge as feasible solutions in the future.
Let’s have a look at the pros/cons of the above-discussed pathway:
Pros | Cons |
Biomass-based, olefin coke, and hydrogen-based blast furnaces pose little to no environmental threat. | The production of green hydrogen is very expensive. Its use is also limited by availability, storage, and transportation. |
Hydrogen as a reducing agent has faster reduction rates as compared to coke. | Hydrogen reduction is endothermic in nature leading to heat shortage in blast furnaces if the hydrogen content is increased. |
Biomass as fuel in blast furnaces has the potential for large scale due to its availability. | Due to the technical limitations of blast furnaces, it appears that coke cannot be completely replaced in the blast furnaces, hence the pathway seems to be less reliable. |
Low carbon feed in steelmaking
In Electric Arc Furnaces, DRI (Direct Reduced Iron), pig iron, scrap metal, sponge iron, etc., are generally used as feedstock for steelmaking. DRI or Sponge iron is generally produced by reducing iron ore, where Hydrogen and Carbon monoxide are used as reducing agents. Due to these reducing agents, carbon dioxide produced during the reduction process is high. (Source)
There are multiple ways to reduce carbon footprints to produce these low-carbon feeds:
- Natural gas-based DR process.
- Syngas-based DR process
- Hydrogen-based DR process (Source)
Let’s have a look at the pros/cons of the above-discussed pathway:
Pros | Cons |
Easy integration with existing infrastructure as only the energy sources for producing DRI are being replaced. | Production costs are comparatively higher than Blast Furnace (traditionally used for reducing iron ore). |
Syngas is easily available as various gasification plants could be used for its production. | Syngas has a large carbon footprint when produced from coal. |
Hydrogen produced from renewable energy-powered electrolysis has almost zero carbon emissions potential. | If renewable sources of power are not used, then high electricity requirements for hydrogen production could lead to potential emissions. |
Green energy for EAF
Electric Arc Furnaces (EAF) produce 28% of the world’s steel (using electricity), though they account for only 8% of the CO2 generated by the steel industry. But, there are growing innovations in using green energy sources that would make EAF completely carbon-neutral.
For example,
- Firstly, by providing carbon-neutral feed to EAF (i.e. iron ore which is provided as a feed to EAF can be reduced with hydrogen while in a solid state producing direct reduced iron).
- Secondly, to power the EAFs, green energy sources (such as tidal energy, wind energy, and solar power) could be used (as opposed to currently used electricity derived from coal or fossil fuels). This would help them become truly carbon-neutral. (Source) (Source)
Let’s have a look at the pros/cons of the above-discussed pathway:
Pros | Cons |
The carbon-neutral power sources (solar, wind, etc.) for EAF can be easily integrated (infrastructurally) with the existing electricity GRID networks. | High capital investments are required to set up renewable energy power plants. |
The technology for various green energy sources has already been established in various environments & industries. | For various carbon-neutral energy sources (such as solar, wind, etc.), there are significant geographical limitations (sunlight intensity, wind speed, etc.). |
Using carbon-neutral solutions (such as hydrogen) can eliminate the use of fossil fuels. | Currently, the production cost of hydrogen fuel is very high |
Alternative graphite electrodes in EAF
Electric Arc Furnaces (EAF) use graphite electrodes in steelmaking. Graphite electrodes act as a conductor for the large electrical currents needed to melt ferrous scrap in the steelmaking process in an EAF. This is due to the electrode’s high thermal conductivity and heat-resistance performance. These graphite electrodes get consumed in the process and contribute to the amount of carbon dioxide being emitted in the process. About 1-2 kg of graphite electrode is consumed per tonne of steel produced, emitting about 4-7 kg of CO2 per tonne of steel (Source).
In light of this understanding, we found that a company started by MIT-based researchers has replaced graphite electrodes with “inert metallic electrodes”, bringing down the CO2 emission to zero through this step (Source) Source.
Let’s have a look at the pros/cons of the above-discussed pathways:
Pros | Cons |
The inert metallic electrode overcomes the CO2 emission that occurs due to the graphite electrode consumption and is scalable for industrial applications. | Production of extremely high amounts of oxygen in the process, which can react with carbon during solidification and form carbon monoxide and blowholes in the cast. |
It can convert even low- and mid-grade iron ore fines directly into high-purity molten iron. | The process/technology is established only in test conditions, and industrial-scale applicability is yet to be established, |
Carbon Capture
In steelmaking, carbon is produced during the oxygen-lancing step. As carbon content is reduced from metal, carbon reacts with oxygen to produce carbon dioxide. There are multiple ways to capture this gas and convert it to useful raw material. This leads to a reduction in carbon footprint.
In one of the solutions, captured gases are sent to a bioreactor where a microbial gas-fermentation biosystem (using acetogenic bacteria) ferments CO-rich gases to produce bioethanol.
Similarly, there are other solutions that install chemical-physical devices having the capability to adsorb carbon oxides from the air. These solutions can be easily integrated into the existing facilities and quickly piloted in a steel plant. Source
Let’s have a look at the pros/cons of the above-discussed technologies:
Pros | Cons |
Easily integrated into existing infrastructure | Expensive storage and transportation |
Testing & deployment is convenient | Carbon emissions are reduced but not completely eliminated |
Technology readiness level is high | Implementation in the steel industry is limited |
Given the extent of CO2 emission from the steel industry, the innovation continues and newer, better technologies are coming up. However, which technology a company should employ depends upon a list of parameters, where one must evaluate every pathway before using it. Some of these parameters are:
- Technology Readiness Level: Technology readiness level is measured from 1 to 9 ( with 9 being a successfully developed solution and 1 being idea conceptualization). The higher the TRL of technology, the close it is to commercialization.
- Feasibility: This parameter involves inspection and availability of raw materials and infrastructure requirements (such as electricity, pipelines, etc.).
- Reduction in CO2 emissions: The amount of carbon emissions from a process is identified and compared with the conventional process already in place, to see whether the extent of reduction in carbon emission justifies the cost
- Integration in existing infrastructure: The technical requirements of the pathway are studied to see if it can be integrated into the existing infrastructure. For example – a company can easily integrate carbon capture systems into the steel industry without making many changes to the existing infrastructure.
- Research intensity: This parameter is helpful in determining whether companies and universities are doing research with respect to a pathway.
Top commercialized technologies for using low-carbon feed in steelmaking
We have discussed briefly multiple ways through which carbon footprint can be reduced to produce these low carbon feed (DRI). For this article, we are going to explore those technologies in detail.
Are you looking for innovation/technologies available in other pathways to decarbonize steel? Fill in the form below, and our researchers will reach out to you to understand your requirements.
Technology #1 – Boston Metal has developed a game-changing Molten Oxide Electrolysis process for making steel
Conventional steelmaking includes iron ore refining and then reduction to iron in a blast furnace which is energy intensive and emits a large amount of CO2. Boston Metal has developed a Molten Oxide Electrolysis technique that significantly simplifies the process and helps reduce CO2 emissions. Let’s see what innovation is happening in this space.
- In their technique, iron oxides are dissolved in a mixture of molten metal oxides such as silica, magnesia, and quicklime in a vessel.
- This mixture is heated to about 1,600 °C by an electric current.
- At the cathode, this current reduces iron ions to form a pool of liquid metal that can be taken to secondary steelmaking directly.
Additionally, Boston Metal researchers have used a 90:10 chromium-iron alloy anode that could withstand the extreme conditions inside the reactor without rusting or reacting with oxygen or the molten electrolyte. So, they have successfully eliminated the need for graphite electrodes in the MOE process. (Source)
According to Boston Metal, Molten Oxide Electrolysis (MOE) cells can be added to achieve a tailor-made manufacturing solution from a thousand to million tonnage output (Source).
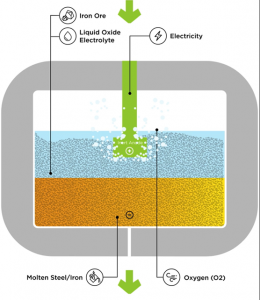
They are also seeking patent protection for this technique in multiple geographies, including India, IN202047015791A (Source).
Technology #2 – Midrex is working on a solution to reduce carbon footprint by using green hydrogen to reduce iron oxide to DRI
Most of the steel currently produced is made via the blast furnace (BF) route or the electric arc furnace (EAF) route. The EAF route contributes significantly less CO2 emissions but is still in the range of 0.5 kg CO2/kg steel. Alternative iron units (AIUs, made from iron ore), such as DRI, hot briquetted iron (HBI), or pig iron, are often required in the EAF to meet quality and productivity targets; these AIUs elevate the CO2 emissions of the EAF.
Midrex (technology leader for direct reduction technologies) is working on a solution to reduce the carbon footprint issue by using green hydrogen (i.e., using hydrogen, where the hydrogen is produced utilizing water generated internally from the process) to reduce iron oxide to DRI. The produced DRI is later sent as feed to EAF for steelmaking.
The system for the direct reduction of iron comprises a process loop using hydrogen as a chemical carrier to remove oxygen from iron ore and regenerate the resulting steam by electrolysis. To capture steam for making Hydrogen, a deduster is used to deduct top gas from the furnace shaft. The steam (water vapor) from the shaft furnace is used for the electrolyzer attached along the process in a loop that produces Hydrogen.
They are also seeking patent protection for this technology (US20200385827A1).
Technology #3 – ΣIDERWIN, a project led by Arcelor Mittal, uses electrowinning for reducing carbon emission
ΣIDERWIN project proposes a breakthrough innovation, compared to the actual steel production process, bringing together steel-making with the electrochemical process. The project has reached technology readiness level (TRL) 6 (Source).
They employ an electrolytic process, flexible enough to be supplied by renewable energies. Their technique transforms iron oxides into iron plates, including those inside the byproducts from other metallurgies. Finely milled hematite ore particles are suspended in a highly alkaline aqueous sodium hydroxide solution at a temperature of 110°C. A current passed through the electrolyte, so the iron metal grows on the surface of the cathode. At the anode, oxygen gas is liberated. The iron plate obtained is fed into an electric furnace to make steel.
The process uses 31% less energy than traditional steelmaking and reduces CO2 emissions by 87%. It eliminates the need for coke production, iron ore processing (the energy-intensive step of pelletizing the ore is eliminated), blast furnace reduction, and basic oxygen furnace refinement. So, it reduces cost and is feasible.
Technology #4 – LKAB, SSAB, and Vattenfall’s HYBRIT project uses sponge iron produced by fossil-free electricity in an electric arc furnace.
The HYBRIT (Hydrogen Breakthrough Ironmaking Technology) Demonstration project aims to revolutionize the European iron and steel industry by replacing fossil-based technologies with climate-neutral alternatives. The project plans to replace the coal-based blast furnace technology with a direct reduction based on fossil-free hydrogen.
The project will produce approximately 1.2 Mt of crude steel annually, representing 25% of Sweden’s overall production, with the potential to avoid 14.3 Mt CO2e of greenhouse gas (GHG) emissions over the first ten years of operation.
In addition, a new, first-of-a-kind hydrogen production facility will be established in Gällivare, using approximately 500 MW electrolyzer capacity powered by fossil-free electricity. The use of this hydrogen (generated by the electrolysis of water and powered by electrolyzers) enables the conversion of iron ore into sponge iron (via Direct Hydrogen Reduction). This process significantly reduces carbon emissions and proposes a new route for processing iron ore. (Source)
Conclusion
The wholesale shift toward the decarbonization of steel may create the largest reallocation of capital in history. The best way to survive is by making asset and footprint decisions today, with a clear road map for the decarbonization of the steel industry.
However, given how huge the steel industry is, a single technology cannot be leveraged to achieve a carbon-neutral steel industry. But, with the help of industry research and market opportunities, first movers can successfully adapt to the decarbonization technology without compromising on production.
If you are looking for a swift transition to decarbonized steel production while safeguarding the steel production license to continue operating in the long term, then GreyB might be the place to look. Get a detailed, customized report on the technologies for the decarbonization of steel and the next innovative step for sustainability. All this with a single click.
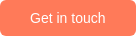