We have tried to describe a problem-solution approach through this case study so that we can convey the advantages of such an approach. An exemplary technology has been used to convey how a problem can be solved using this approach.
Joe – A Senior researcher at one of the largest chemical companies in the US had been under a lot of stress lately. Joe was looking for solutions to a problem which affected an entire industry whose market was valued at USD 7.87 Billion in 2015 and is projected to reach USD 15.76 Billion by 2026, at a CAGR of 6.6%.
We are talking about Pressure-sensitive Adhesives.
For those unaware, Pressure-sensitive adhesive (PSA) is a type of adhesive that forms a bond when pressure is applied to marry the adhesive with the adherend. No solvent, water, or heat is needed to activate this sort of adhesives.
The PSA market had seen a huge growth, which could be primarily attributed to its increasing demand in diverse industries such as packaging, automotive & transportation, and electronics, electrical & telecommunication, etc.
Coming back to the problem, it needs to be stated that selecting the appropriate adhesive for a particular application can be quite a challenge.
Depending on varying application requirements and end-use environmental conditions, one has to decide whether to use a natural or synthetic rubber (SBC, SBR) -based adhesive, an acrylic adhesive or silicone adhesive. If judged on the basis of overall cost and performance, definitely, solvent acrylic PSAs provide a wider range than other adhesives in terms of durability, resistance to aging, temperature flexibility.
In other words, acrylate adhesives can serve as the best option, except for the fact that these adhesives normally don’t have good temperature resistance
If that problem could be solved, Acrylate adhesives have the potential to become the go-to product in the market.
Joe was looking for solutions to this very problem and spent a considerable amount finding solutions.
Our research team started on the task of finding all the available research done in the domain that could solve this specific problem. After spending a considerable time, we collated all the results and sent them to Joe.
We know a lot of people would be looking for solutions to this very problem, therefore, we have shared three solutions that can help you solve this problem.
Side note: This is how we helped Todd, an R&D team lead,: Todd, Here are Ways To Increase Carbon Content in Direct Iron Ore
Leveraging Benzoxazine:
According to a patent, we got our hands on, the problem can be curbed by introducing a composition of benzoxazine (1-65%) and the reactive Glycidyl methacrylate (GMA) (35-99%) having a glass transition temperature Tg of −35° C. to 32° C. and having a reactive functional group which can react with benzoxazine to form an interpenetrating polymer network.
Introducing Mixture of Different Monomer Groups
By introducing a mixture of the different functional group containing monomers in a specific ration, the problem can be curbed. The monomers are: acrylic esters of the formula CR3 2═C(R2)(COOR1) (5 to 100 wt %), where R1 is a branched alkyl group having 16 to 22 C atoms and has at least two branching locations, R2 is selected from H, methyl or halogen, and R3 independently at each occurrence is selected from H or halogen,
- acrylic esters of the formula CR3 2═C(R2)(COOR1) (5 to 100 wt %), where R1 is a branched alkyl group having 16 to 22 C atoms, and has at least two branching locations, R2 is selected from H, methyl or halogen, and R3 independently at each occurrence is selected from H or halogen,
- acrylic esters of the formula CR6 2═C(R5)(COOR4) (0 to 95 wt %), where R4 is a linear, singly branched, cyclic or polycyclic alkyl group having 1 to 14 C atoms, R5 is selected from H, methyl or halogen, and R6 independently at each occurrence is selected from H or halogen,
- other monomers having OH, COOH, epoxy, etc. functional groups (each 0 to 5 wt %)
Using A Particular Substrates
Taking the substrate or backing material polyethylene (PE) resins or polypropylene (PP) resins. More specifically, if the substrate has a composition comprising 50% by weight or more PP resin, that is specifically good for heat-resistance. Additionally, this solution also discusses a combination of two monomers to be used with the substrate –
- an alkyl (meth)acrylate (50 to 99.9% by weight) with formula – CH2═C(R1)COOR2 (R1 is H atom or CH3, and R2 is an alkyl group with 1 to 20 carbon atoms),
- a carboxy group-containing monomer (0.1 to 5% by weight);
Researchers in R&D spend a lot of time studying research papers but search within patents does not yield similar output as we get in journals. Therefore, in the majority of the cases, search within patents is not fully explored. Therefore, we found that if the researcher can combine his journal research with an expert patent search many new solutions can be identified.
By the way, If you are researching in PSA domain and looking for solutions to problems like:
- How to increase the thermal stability or operation temperature range of PSA?
- How to increase the tackiness?
- How to increase the range of materials to which the PSA can stick to (surface energy problem)?
- How to increase solvent/UV/Ozone resistance in PSA?
We will be able to help you out. Let’s chat:
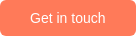
Analysis By: Arindam Som, Group Manager, Operation
Read Next: How Competitive Analysis Can Help R&D Team Innovate Better?