Despite the EV industry’s rapid growth over the past decade, it still has some areas for improvement. Companies are constantly innovating in these areas so that a reliable EV experience can be possible without concerns about battery life, charging, and range. Battery charging and thermal management are two of the top EV industry trends. Companies and startups are implementing new semiconductor and battery cooling techniques to solve the EV battery issues.
Companies are also working on electric machines, key components of electric vehicle drivetrains. In recent years, most traction drive systems have converged using a permanent magnet machine.
A growing trend is toward enhancing traction machines’ power density and efficiency. Resulting in creative designs, improvements to fundamental machine topologies, and the introduction of new classes of machines. These innovations are taking the EV industry by storm. So, in this article, we decided to talk about the top 7 battery and electric machines-related innovation trends in the EV industry. Let’s jump right in!
Further, we also have a detailed EV Research Trends and Analysis Report that you can get by filling out the form below:
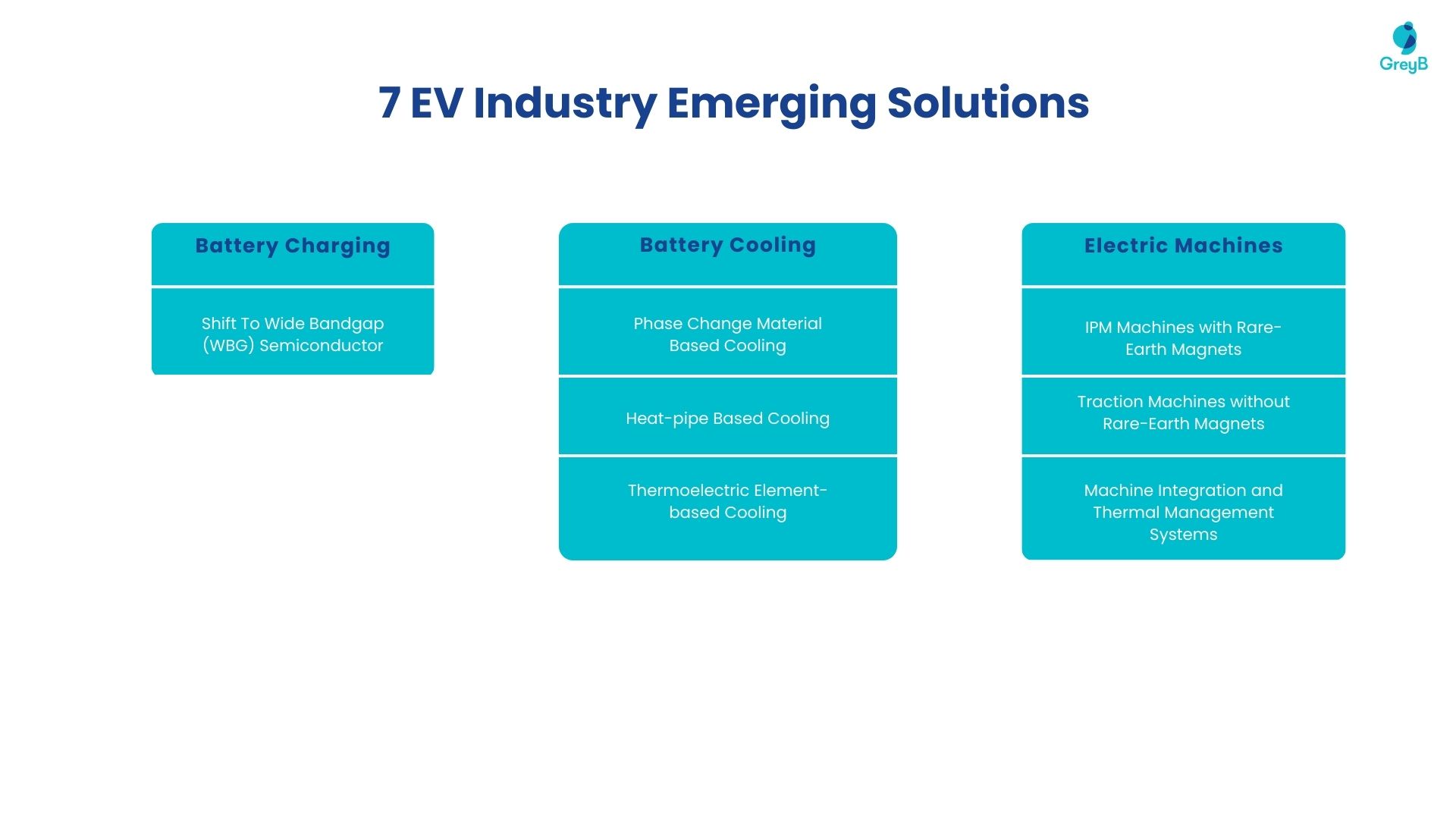
EV Battery Charging System Solutions
1: Shift To Wide Bandgap (WBG) Semiconductor
Wide Bandgap Semiconductors have larger bandgaps than conventional semiconductors. Conventional semiconductors like silicon have a bandgap in the range of 1 – 1.5 electronvolt (eV), whereas wide-bandgap materials have bandgaps in the range above 2 eV.
Electric vehicle and hybrid EV developers seek effective power solutions for several propulsion stages. Wide-bandgap semiconductors like silicon carbide (SiC) and gallium nitride (GaN) outperform silicon in various ways, including improved efficiency and switching frequency and the capacity to endure increased operating temperatures and voltages.

Automotive power electronics developers need GaN and SiC devices, as well as a redesigned powertrain architecture that can match the efficiency and power density needs of electric vehicles, to enable quicker charging. Batteries require a high energy storage density. The autonomy of an electric vehicle is directly proportional to the efficiency of its powertrain system. To attain the greatest driving range per charge for the given battery capacity the entire energy conversion chain must be as efficient as possible.
In comparison to silicon, silicon carbide (SiC) has a substantially wider bandgap of 3 electron volts (eV) and a much greater thermal conductivity. Additionally, silicon carbide power semiconductors device characteristics such as the RDS (on) rise less with temperature. This enables designers to operate within narrower margins or at greater temperatures in their wide bandgap power electronics designs, resulting in increased performance.
Infineon’s CoolSiC solutions combine breakthrough technology with benchmark dependability for their client’s success and are based on established, high-quality volume production.
GaN has an even bigger bandgap (3.4 electronvolts) and much greater electron mobility than SiC. The breakdown field is 10 times greater than that of silicon (Si), and electron mobility is twice. GaN wide bandgap semiconductor power devices are the preferred technology in contemporary resonant topologies, providing novel techniques such as new topologies and current modulation.
CoolGaN devices from Infineon focus on excellent performance and resilience while bringing substantial value to a wide range of wide bandgap semiconductor industries such as server, telecom, wireless charging, adapter, charger, and audio.
Silicon Carbide (SiC) and Gallium Nitride (GaN) are next-generation semiconductors for increased power conversion and electric vehicle applications. These Wide BandGap materials will power potentially high applications such as solar and wind power, vehicle electrification, cloud computing, EV charging, and 5G communications. ON Semiconductor, a prominent manufacturer of power management devices, is creating a complete ecosystem of parts to enable wide bandgap power designs, including SiC diodes and SiC MOSFETs, GaN HEMTs, SiC and GaN drivers, and integrated modules.
EV Battery Cooling Technology Solutions
2: Phase Change Material Based Cooling
A thermal runaway is a chain reaction in which an increase in temperature produces additional temperature increases and uncontrollable energy release. Lithium batteries are especially vulnerable to thermal runaway occurrences due to a variety of factors. This includes their high energy content and proclivity to self-heat once the electrolyte reaches a specific temperature (70° to 130° C). As a result, heat control of an EV battery pack is critical. Engineers that create energy-dense packs must use strong cooling systems, which are frequently composed of liquid cooling loops with channels. The intricacy of these systems adds around 10-20% to the overall cost of the battery pack.
A phase-change material (PCM) is a substance that absorbs a considerable quantity of heat energy while transforming from solid to liquid and then releases the energy while turning back into a solid.
Companies And Startups Working on Phase Change Material-Based Cooling
AllCell Technology
The patent applications for PCM usage in thermal management of lithium-ion batteries, ultracapacitors, and fuel cells are held by AllCell Technologies. The company’s preferred PCM is a graphite composite material, which is a blend of wax and the same component found inside pencils.
AllCell’s passive heat management technique is based on the utilization of Phase Change Composite (PCC). PCC wraps each lithium-ion cell, absorbing and transmitting heat away from the cells to significantly improve cell life by preventing fire or damage to the cell. AllCell is currently creating battery packs for light EVs such as motorcycles and scooters using their PCM technology.
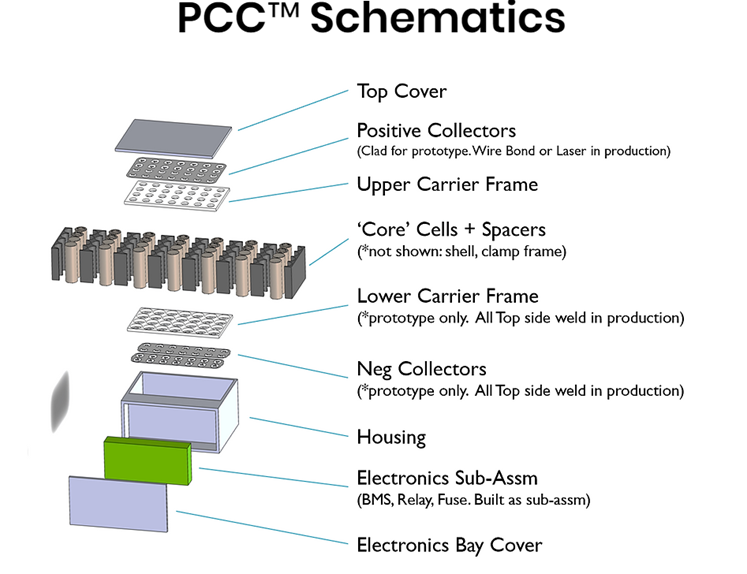
Advanced Cooling Technologies Inc
AdvancAdvanced Cooling Technologies has different types of products for different industries. For EVs, it has many solutions including PCM heat sinks. The heat sinks or modules as per ACT are an ideal solution for the Spacecraft market. It could be used for applications such as missiles that have finite mission life and can utilize PCM energy storage to replace complex active thermal management solutions.
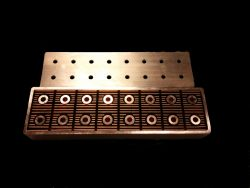
3: Heat-pipe Based Cooling
The battery used in an electric vehicle determines its performance. During the operation of an electric car, batteries endure rapid heating, particularly at the start of charging, which might result in a fire. Using a heat pipe and a Phase Change Material (PCM) to cool the battery can prevent this. While the heat pipe is responsible for transferring the heat energy from the battery, PCM functions as a heat sink when the battery runs. This makes the battery’s performance stable and extends its lifespan.
Heat pipe and PCM provide benefits such as high efficiency, ease of use and integration, the ability to lower battery temperature uniformly, and the ability to be used for more than 20 years.
The heat pipe is a closed tube made up of three parts: the evaporator, the adiabatic section, and the condenser. According to a study released by E3S Web of Conferences, the use of the heat pipe, as well as heat pipe and PCM for battery cooling systems, would greatly reduce the temperature on the battery’s surface. If just the heat pipe is used, it is caused by heat absorption by the evaporator. Meanwhile, when a heat pipe is paired with PCM, the temperature drops as well. As a result, the outcome is better than when simply a heat pipe is used.
Companies And Startups Working on Heat-Pipe Based Cooling
Allatherm
Heat loops are the next technical step after heat pipe assemblies superseded the archaic, heavy, and inefficient solid metal heat sinks in computers.
Heat Pipes and Heat Loops are heat superconductors. Today no one alternative heat transfer device can be as efficient as a Heat Pipe/Loop. And Allatherm is one of the companies using the technology for better thermal management.
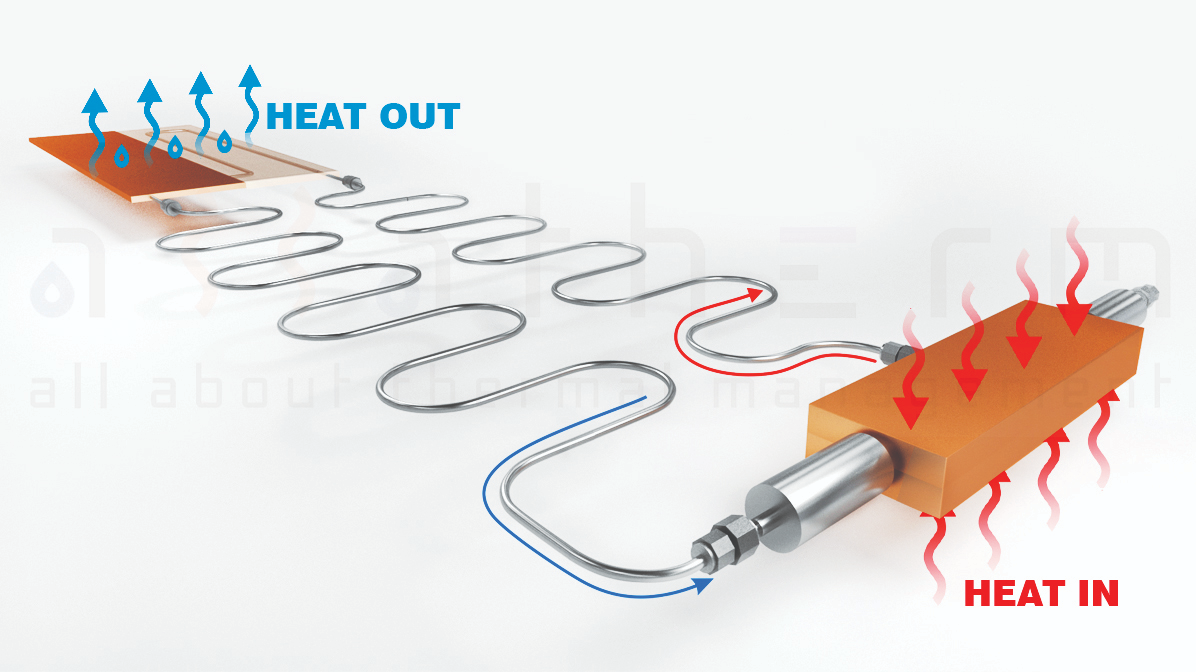
Allatherm’s HPCS-HP-45 is a heat pipe charging system for charging stations. It is a small volumetric fluid dosing device used to charge two-phase heat transfer systems such as heat pipes, loop heat pipes, and thermosiphons with high-pressure fluids (Tboil<30 °С).
Allatherm Heat Pipe Charging Stations (High Pressure and Low Pressure)
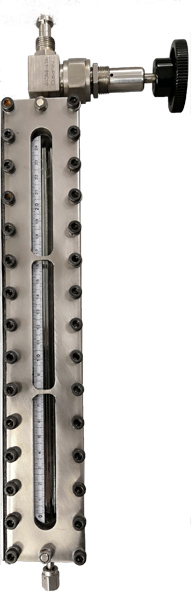
Advanced Cooling Technologies Inc
Advanced Cooling provides many heat pipe products for thermal management. ACT made Copper/water heat pipes that are made of copper which typically operate in the temperature range of 20 to 150°C. They are cost-effective and their effective thermal conductivity ranges from 10,000 to 100,000 W/m-K, and the heat transfer is one-dimensional.
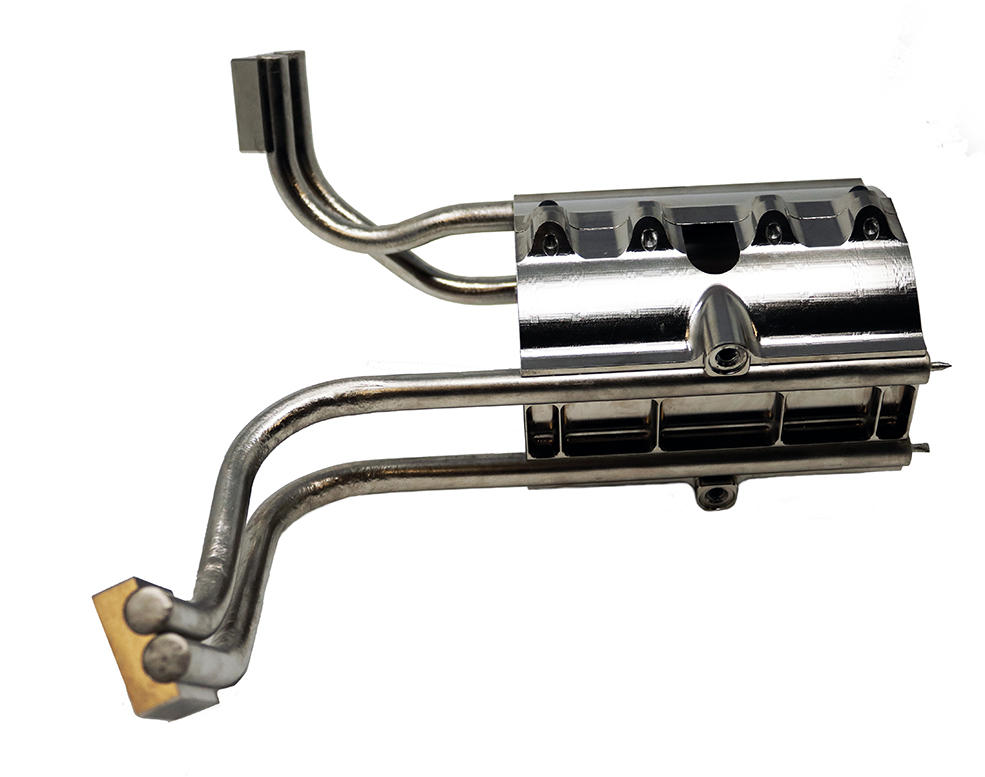
4: Thermoelectric Element-based Cooling
The temperature has a considerable impact on battery operating performance and capacity. In other words, the temperature has a substantial impact on both discharge capacity and charge. The pace at which the automobile uses energy and the rate at which it charges. The greater the rate of charging or discharge capacity of a battery, the greater the temperature increase. Hence, a precise balance must be found between charge/discharge rate and capacity.
Temperature is another stress element that reduces the capacity of a lithium-ion battery over time; this phenomenon is known as ‘capacity fade,’ and it affects an EV’s long-term performance.
Another type of thermal management that has sparked ripples across the automobile industry is Thermoelectric Coolers, which place semiconductors between the source of heat (the battery) and a heat sink.
The incentive for using thermoelectrics lies in their compact size, lightweight, high reliability, and sub-ambient cooling.
When a voltage is provided, a temperature difference between the sink and the source is created, implying that heat transfer occurs via conduction. This allows for precise temperature control with a simple adjustment in voltage. And in circumstances when heat is required, the direction of heat transmission may be modified by reversing the current.
Companies And Startups Working on Thermoelectric Element-Based Cooling
3M
3M applies temperature management technology to aid in the development of xEV battery designs. Thermal insulation helps to control operational temperatures in difficult situations by blocking temperature extremes. Dielectric fluids from 3M aid the management and regulation of heat transfer in batteries built for direct contact cooling.
The company offers a wide range of thermal management solutions for xEV batteries in pouch, prismatic, and cylindrical forms. 3M Boron Nitride Cooling Fillers comprise ceramic fillers that enhance conductivity while retaining electric insulation in polymers. Boron nitride-filled compounds may potentially enable lighter, simpler component designs, lowering overall system costs by functionally combining heat control with electrical insulation.
Ferrotec
Ferrotec has a 36% share of the global thermoelectric module market. In 2018, Ferrotec expanded its TEM business into the automobile sector for specific applications such as cooling and heating of batteries in electric and hybrid vehicles. Ferrotec’s high-performance thermo-electric modules are custom-designed devices offering highly responsive temperature control to within 0.1 degree Celsius.
Ferrotec offers a wide variety of thermoelectric cooler sizes and power handling options.
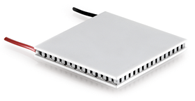
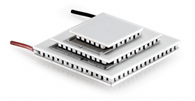
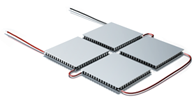
EV Electric Machines Trends
5: IPM Machines with Rare-Earth Magnets
In recent years, the emerging hybrid and electric vehicle market, and, to some extent rising rare-earth magnet costs, have boosted demand for interior permanent magnet (IPM) motors. With advantages like near-constant power over a broad speed range and a magnet-retaining design, IPM motors are ideal for applications like traction motors and machine tools.
The Interior Permanent Magnet (IPM) machine’s capacity to generate permanent magnet torque and reluctance torque, as well as perform a broad CPSR operation, has significantly boosted its desirability for traction drive systems.
IPM machines can be built to generate reluctance torque in the 40%–50% range, or even higher. This appealing characteristic has made IPM machines the machine of choice for many applications. And this trend is likely to continue since the cost of magnets accounts for around 20%–30% of the cost of the motor, and manufacturers are interested in lowering the cost of the motor.
The rare-earth-based, hard magnetic material Neodymium Iron Boron (NdFeB) in particular has provided considerable performance gains not feasible with other technologies, allowing the creation of small, torque- and power-dense electric traction motors.
Companies working on IPM Machine
Benevelli Group
Electric motors manufacturer, Benevelli Group, manufactures IPM machines for EVs with 20 experience in powertrains. The company understands the benefit of IPM machines over SPM (Surface Permanent Magnet) machines.
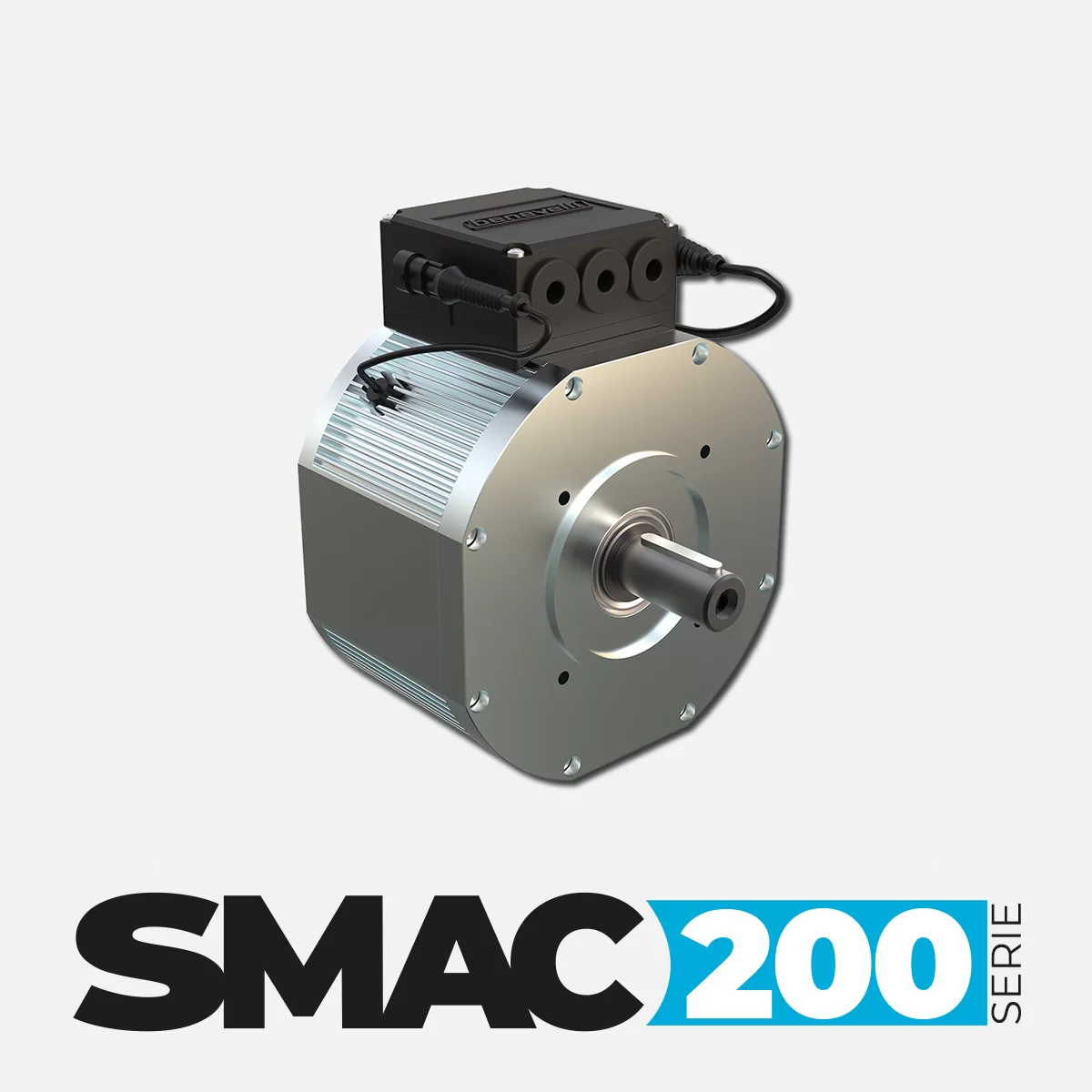
6: Traction Machines without Rare-Earth Magnets
The simultaneous attempts for non-rare earth machine alternatives are an important trend in the design of machines for EVs. By removing the rare-earth magnets, not only are motor costs reduced but the reliance on this key element is removed. Induction machines have had a decent chance at addressing this need. But the rising demands for high specific power and power density are removing them as viable possibilities.
Synchronous reluctance machines (SynRM) are intriguing because of their resilience, high efficiency, minimal torque ripple, and simplicity (cheap cost) of control. However, they have significant drawbacks. Such as a lower power factor, which affects converter sizing and cost, and, more critically, a restricted CPSR. Even the SRM (Switched Reluctance Motors) has severe noise difficulties, as well as excessive torque ripple and vibration, plus substantial control complexity and expense.
SynRM (Synchronous Reluctance Motors) without magnets, when properly constructed, could work as a highly appealing low-cost machine from both the motor and inverter perspectives. With more investigation, SynRM and SRMs can give a road to high-performance traction machines without using rare earth elements. Improved SRM and SynRM research may be helpful to for non-rare-earth or decreased rare-earth drivetrains. (Source)
Companies that use Motors Made without Rare-Earth Magnets
Tesla
The use of induction machines is everywhere in industrial automation, but not so in the automotive industry. The key exception here is Tesla uses induction machines made from copper rotor cages in all of its vehicles. Earlier, they licensed this technology to Toyota but afterward, they announced to license it at zero cost.
Renault
Wound motors include copper windings in place of permanent magnets on the rotor. Working with German company Continental, Renault has successfully used wound motors in cars, including the Renault Fluence and Renault Zoe.
7: Machine Integration and Thermal Management Systems
Integration of machine and power electronics is another growing trend that is bound to continue. Powertrain equipment must become more compact as space requirements for vehicle comfort rise. As a result, the new integration approaches become increasingly crucial.
The concept of physically integrating the electric machine and power electronic drive into one enclosure (package) provides many benefits. These include compactness or decreased size, simplicity of installation, reduced number of parts, shortened cable lengths, and busbars. All of this might result in desirable technical benefits such as decreased electromagnetic interference, lower voltage overshoots at motor drive terminals, and considerable cost reductions.
It is expected that combined motor and power electronics can enhance power density by 10%–20%. While lowering manufacturing and installation costs by 30%–40%. The co-location of an electric machine and power electronics in the same box, on the other hand, offers considerable hurdles for the combined system.
As a result, putting these two components in a single packaging presents a challenge. These issues have been researched in order to produce realistic and novel solutions that capitalize on the benefits of integration while reducing system faults.
The integration of motor and power electronics can be seen in Chevy Volt 2016 and Tesla Model S.
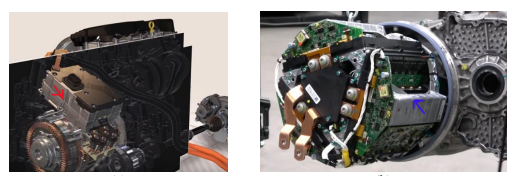
Conclusion
The landscape in these segments will become more competitive this year. With the arrival of new players, acquisitions, and the constant influx of new innovation by EV giants to maintain their footing, industry competition is real and worth putting your name into!
But to establish a stronghold, you first need to know the competition and what they have been up to:
What trends are they working on? What technologies are they adopting or innovating? And what solutions are they offering to their consumers?
Now, that’s not read-and-go content. To strategize your R&D plan for the year, you need to go back and forth to analyze this information.
Our intelligence analysis not only sheds more light on the EV industry’s primary, secondary, and tertiary trends but also discusses various company-specific insights that you won’t want to miss. So, if you are interested in any particular information about EV innovation trends, market research, competitive analysis, and patent intelligence, fill out the form below, and we will help you make better business decisions.